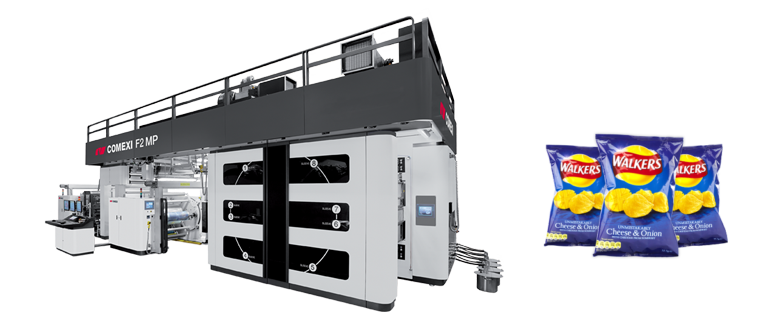
The Comexi F2 MP press has been designed to satisfy the print needs of the longest runs in the flexible packaging sector for the retail and wholesale channel.
The Comexi F2 shares the patented FLEXOEfficiency concepts of ergonomics and accessibility, as well as the performance and robustness of the rest of the F2 range. All combined with a drying system design for the best drying performance and a reinforced design for the printing units at a maximum speed of up to 500 m/min for runs where the print speed is the differentiating factor.
Main benefits for you
Faster setpoints, less shrinkage, more benefits. The job changeovers in flexo presses generate waste in web and inks that have a significant impact in the profit and loss account. The current trend to reduce runs implies more changeovers, an increase in the total waste generated during the setpoints and a loss in machine efficiency.
At Comexi we have launched a set of solutions that adapt to the difference scenarios facing our clients. The CINGULAR MODULES offer automatic and semi-automatic features, with or without a mark, adapted to the specific requirements of our industry.
Excellence with the most efficient cleaning system : The Comexi SelfCleaning is an automatic system that manages the ink supply to the print, and cleans the ink chamber, the anilox, ink tanks and connection hoses in the circuit.
The system adapts to water-based inks and solvent-based inks. Its high level of automation makes it possible to program different cycles (from light to intensive) to adapt solvent and time consumption to your needs. These advantages combined with the easy use thanks to the simple interface, complete a system designed according to the highest standards of efficiency.
The design of the Comexi F2 MP printing unit is reinforced with respect to its siblings in the range, since it has larger diameter bearing supports, and large diameter bearings. It is fitted with a series of carbon fibre shafts both in the PC and in the AX. The PC ones are hydraulic for using hydraulic intermediate carbon fibre sleeves.
The combination of these supports and shafts in carbon fibre offers greater robustness against the impacts inherent in flexographic printing, and makes it possible to obtain a high quality print at a greater speed.
The press has 8 decks adapted for a front print. Its design adapts to the easy access requirements for maintenance and daily operation thanks to the FLEXOEfficiency concept.
The doctor blade is assembled in a closed swinging chamber mounted on linear guides, with automatic horizontal movement by means of low friction, pneumatic pistons.It is dismantled easily without having to disconnect the inking tubes, facilitating the cleaning and changeover tasks, with simple handling thanks to its extraordinary 12 kg weight.
Thanks to the patented ComexiMAGNETBlade technology, a tool-free magnetic changeover system, we can obtain a fast and safe blade and seal changeover.
The plate cylinder and anilox sleeve changeover takes a couple of minutes. The covers are opened manually, in a quick, simple way.
The drying equipment is made up of two fully independent circuits which, via two blowers, blow hot air at high speed, evaporating the solvent or water contained in the ink. The first circuit is used to dry between printing units. The screen can be removed freely from the machine by disconnecting the tubes from the inside, and the housing includes an inspection door, so maintenance is comfortable and easy. Both concepts are patented by Comexi.
The second corresponds to the drying tunnel, which is 5 m long. It is made up of sixteen drying boxes each one with a blower nozzle, with tubes arranged to optimise heat loss. The screens can be dismantled easily and do not need tools for cleaning. The tunnel includes an specific opening for maintenance and cleaning.
The Comexi F2 MP represents excellence in ergonomics and usability. It is fitted with a top diaphanous platform which provides access to all the elements requiring maintenance, highlighting the access to the set of rollers at the tunnel exit.
You will find several details that highlight this machine as the best solution in terms of maintenance: its easy handling and doctor blade access, filter change, greasing points, decentralised electronic panel, and others.
The press is designed so that most of the functions can be controlled from the control console. In parallel our COMPACT concept, based on the SIMOTION platform and in decentralising the electronics, provides for high electronic integration, thereby eliminating electronic equipment containers and facilitating maintenance tasks.
At Comexi we apply the DDDrive concept for driving the shafts via AC motors without any kind of mechanical transmission, controlled by absolute encoders coupled directly to the shafts. All improving the register and, consequently, the quality of the print.
You will obtain production data for subsequent analysis such as the amount of meters printed, the amount of meters lost, the job duration time, stop times, print times, average real speed, etc.
With the operator attributing the cause of the stop, statistics are obtained on the various causes of stops and the time assigned to each one. All the data can be stored in the computer memory and/or in external data storage devices.
Work files can be created to increase the efficiency in the job changeovers, and these files can be recovered subsequently.
The ENERGYSavvy concept, applied to a set of electrical and electronic control technologies, saves large amounts of energy and drastically reduces CO2 emissions.